What are ultra-high temperature materials
Ultra-high-temperature materials refer to the most heat-resistant high-grade materials that can be used as usual under severe environments such as stress and oxidation, and at an ultra-high temperature of about 2000°C.
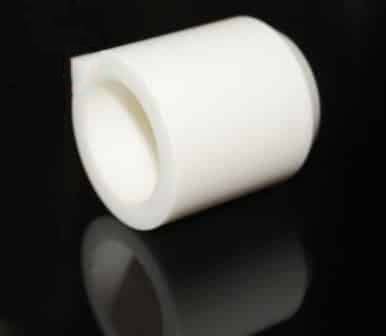
Research and application of ultra-high temperature materials
1. Refractory metal
Refractory metals (W, Mo, Ta, Nb, Zr, etc.) and their alloys have outstanding advantages such as high melting point, high temperature resistance and strong corrosion resistance. The application fields involve solid-liquid rocket engines, re-entry spacecraft and aerospace nuclear power System and so on.
2. Ceramic matrix composite materials
Ultra-high temperature ceramic materials, especially the borides and carbides of the insoluble metals Zr, Hf, and Ta, represent candidate materials that can be used above 2000°C. They have excellent physical properties, including rare high melting points, high thermal conductivity, and high Elastic modulus, and can maintain high strength at high temperature, but also has good thermal shock resistance and moderate thermal expansion rate, it is the most promising material in the field of ultra-high temperature in the future.
(1) Carbide ceramic matrix composite material
The melting points of hafnium carbide (HfC), zirconium carbide (ZrC) and tantalum carbide (TaC) are much higher than their oxides. They do not need to undergo any solid phase transition, and have good thermal shock resistance. Has high strength. The fracture toughness and oxidation resistance of this type of carbide ceramics are very low. In order to overcome the brittleness of ceramics, fibers are usually used to enhance toughness. In 2000, NASA conducted arc heater ablation tests on 13 material systems of the X-43A (Mach 7) nose cone and leading edge produced by different companies that may be used in the Hyper-X program. The results show that the carbon fiber reinforced HfC-based composite produced by RCI has the best effect. It completes all 10 cycles of 10 minutes, with a mass loss of 1.30% for 3 cycles, a mass loss of 3.28% for 5 cycles, and a mass loss of 10.33% for 10 cycles; After completing the continuous heating for 1 h, the mass loss was 1.12%.
(2) Boride ceramic matrix composites
Research shows that the brittleness and room temperature strength of ZrB2 and HfB2 based ceramic composites can be overcome by reasonable selection of the composition, purity and particle size of the raw materials. Their strong covalent bond determines that they are difficult to sinter and densify. In order to improve its sinterability and density, it is possible to increase the surface energy of the reactants, reduce the grain boundary energy of the product, increase the bulk diffusivity of the material, delay the evaporation of the material, accelerate the transfer rate of the substance, and promote the rearrangement of the particles. And improve the mass transfer kinetics to solve.
(3) C/C composite material
C/C composite material has light weight, high specific strength, high specific stiffness, high modulus, low thermal expansion coefficient, high strength at high temperature, good ablation performance and creep resistance in a large temperature range, and good resistance Advantages such as thermal shock performance.
From room temperature to 2 000 ℃, the strength of C/C composite material increases with the increase of temperature, and it still has higher strength at 2500 ℃. Compared with many metal alloys and ceramic matrix composites, C/C composites have the highest specific strength, but their applications as high-temperature structural materials are extremely limited. This is because in an oxidizing environment, especially over 350℃, its use effect Very bad, it will burn above 500°C. Therefore, the development of a reliable oxidation protection system is critical to the full potential of C/C composites. To this end, many research institutions have conducted in-depth research on this issue, such as by adding SiO2, ZrO2, Al203, etc. to the substrate and improving the surface coating to study the impact of oxidation resistance. The United States, Russia, France and other countries have proposed to use refractory carbide coatings in recent years to improve the oxidation resistance of carbon-carbon composites, reduce the ablation rate, and withstand higher gas temperatures or longer working hours. The molten carbides include SiC, HfC, TaC, NbC, ZrC and so on.